Sustainable Concrete
Inspiring to Build Better
According to the latest UN (United Nations) forecasts the world's population will reach 9.7 billion by 2050, up from over 8 billion today. In addition, society is becoming increasingly urban with cities growing faster than the general population.
The world of tomorrow will be determined by population growth, urbanisation and economic progress. This will increase demand for new buildings and infrastructure and consequently, for concrete. Centralisation and densification of the growing population will increase the need for new high-rise buildings as well as for gigantic construction and infrastructure projects.
Concrete sets the standard for many structures with its unique mechanical properties, such as strength, durability, availability, ease of handling and formability. It will consequently remain an indispensable part of any new construction for the foreseeable future. One area of growing concern for environmental leaders is CO2 emissions. Like all building materials, concrete has an environmental footprint and is often described in terms of greenhouse gas (GHG) equivalents. Second only to water, concrete is the most used material on the planet representing about 50% all man-made materials by mass. Because society consumes so much concrete*, even small changes to its formulation can dramatically affect the construction industry’s annual carbon footprint to benefit everyone.
The construction sector is facing the challenge of committing to sustainable construction while coping with tight time schedules, meeting high-quality standards and improving cost efficiency all at the same time. The pressure to improve processes is growing continuously and requires special concrete admixtures to overcome these obstacles. Over the years, we at Master Builders Solutions have proven that our innovations can support and contribute to sustainable solutions that meet the challenges and demands of our customers and the construction industry in general.
Our most recent groundbreaking advancement, MasterCO2re, is designed for the production of low-clinker concrete.:
1. What is Concrete?
From material composition to alternative materials to durability.
Concrete is by far the most widely used building material in the world because it combines durability, strength, and ease of processing. In its fresh state it can be formed into any shape before it hardens and acquires a high compressive strength. Due to its properties, concrete is a versatile and durable building material that easily withstands temperatures from hot down to sub-zero. Its constituents' almost unlimited availability and recyclability make concrete an indispensable building material today and in the future.
Concrete consists of cement, aggregates, sand, and water in its simplest composition.
Aggregates make up about 70% of concrete. They are usually sourced from local deposits and added to the concrete mix in different particle sizes. Gravel, crushed rock, or even crushed, recycled concrete are considered aggregates with the advantage of conserving natural resources.
Sand is a unique subcategory of aggregates. In standard concrete mixes, it accounts for about 50% of the total weight and is only acceptable in diameters of less than 2 mm. However, the supply of sands suitable for concrete is becoming increasingly difficult as they becoming ever scarcer.
Cement is the most crucial constituent as – together with the water – it forms the glue or paste that combines the main components - aggregate and sand- to create the artificial rock that we call concrete. The dilemma is that the lower the water content, the harder it is to manipulate the concrete in its fresh state but lower water content is desirable because the hardened paste is denser and more durable due to its improved adhesion to the aggregates. The amount of water in concrete, to a greater extent determines properties such as workability, compressive strength and durability.
Composition of concrete in volume and weight
Admixtures are used to enhance or modify concrete which enables the use of locally sourced materials whilst maintaining the quality of the concrete. Small doses of chemical admixtures are added to the concrete during mixing to improve workability, placement and final hardening properties. Our concrete admixtures make many things possible, for example pumping concrete vertically 540 meters high as we did during the rebuilding the World Trade Center in New York. They also enable the recycling of returned concrete and alternative materials in new concrete mixes and they even make the pouring of concrete in freezing conditions possible.
The main impact categories of admixtures are:
-
Water reduction through MasterGlenium
-
Water retainment using MasterPel
-
Air entrainment with MasterAir
-
Accelerate and delay setting times with MasterSet
-
MasterLife WP is a water repellent
-
Modify viscosity with MasterMatrix
- Improve workability of sprayed concrete by adding MasterRoc HCA
Fluid concrete admixture mixed in the concrete
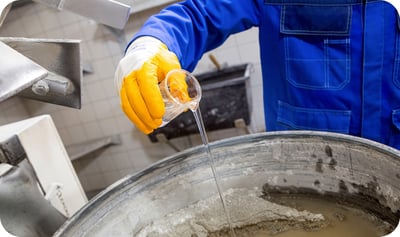
1.1 Why does traditional concrete have a large carbon footprint?
Despite all its excellent properties, concrete casts a shadow: it is responsible for 8% of annual man-made global CO2 emissions, 90% of which can be attributed to the production of cement clinker. Cement clinker is the strength-providing component of cement and its production is very energy intensive. It causes excessive carbon emissions from the burning of fuel to generate heat (2,300° to 3,000° F (1,260° to 1,650° C) which is needed to facilitate the chemical process called calcination. Grinding the clinker to a (cement) powder requires further electricity consumption. The highest contribution though, stems from the CO2 emissions released as part of the decarbonisation of limestone during calcination.
Increasing energy costs have led to substantial increases in cement manufacturing costs and since 2021, have driven the inflationary pressure on construction material prices. The CO2 emissions certificates trading scheme has had an insignificant impact on cement costs as the energy-intensive cement industry is exempt for now. This will change however when the exemption for cement production is progressively phased out between 2026 and 2034. By coincidence, a decrease in the proportion of cement clinker in cement will not only be beneficial from an ecological perspective, it will also be welcomed by the concrete value chain from a commercial point of view.
The cement clinker production process:
Master Builders Solutions has a history of supporting the concrete industry with the introduction of new cement types whilst ensuring that the strength and durability of the ensuing structures is maintained. Low clinker cement is no exception and concrete producers will continue to benefit from the newest technologies and developments in this field.
1.2 Supplementary cementitious materials (SCMs)
Adding supplementary cementitious materials or SCMs to cement or concrete can contribute positively to the properties of the hardened concrete including durability, whilst also replacing clinker to reduce CO2 emissions significantly.
Experience the Success Story of Promsa - Cementos Molins:
Common SCM types for the manufacture of cement and concrete are:
-
Ground granulated blast furnace slag from iron production,
-
Fly ash from energy production in coal-fired power plants
-
Silica fume from the production of silicon or ferrosilicon metal
-
Limestone filler from the grinding of naturally occurring pozzolana and calcium carbonate is becoming increasingly popular
-
Calcinated clays, produced by the calcination of common clays or shales
If we look at the mechanical properties of concrete, there are two main weak points: low tensile strength and brittle behaviour. The tensile strength of concrete is usually only about one-tenth of its compressive strength; when the tensile strength is exceeded, the concrete will fail suddenly and without warning. On the other hand, steel can absorb high tensile stresses and displays ductile behaviour. This is why steel rebar or mesh is the primary reinforcement material in concrete, forming an extraordinary composite material which counters both tensile and compressive forces equally well.
The embedded steel is protected from corrosion due to the alkaline environment in concrete. However, reinforced concrete must crack to activate tensile forces and in addition, concrete absorbs carbon from the environment which leads to a loss of alkalinity, initially at the surface but later throughout. If these cracks become too wide or the carbonation front reaches the embedded reinforcing steel, it will lose its protection and corrosion will occur. Consequently, rust will expand the reinforcement steel which will lead to spalling of the surrounding concrete, and the destruction of the integrity of the structure.
Durability, or the resistance and insensitivity of the building material to environmental influences (e.g., moisture and temperature) is one of the essential requirements for concrete because it determines the service life of any given structure. With clever structural design, correct positioning of steel reinforcement, well-designed concrete composition, proper execution, appropriate curing measures and regular maintenance, concrete is an exceptionally durable building material with an expected service life of at least 50 years for a positive impact on sustainability. Infrastructure such as bridges, dams or tunnels are designed for a service life of 100 years or longer.
1.3 Related blog articles
2. Challenges Facing the Concrete Industry
Looking at the big picture, the global trend towards sustainable construction and the corresponding need to reduce CO2 emissions is of vital importance for the environment. Around two-thirds of building-related emissions stem from operations (heating, cooling, lighting), and one-third relates to the carbon bound in the building materials'. Accordingly, the focus of regulatory measures has been on improving energy efficiency. Therefore, as energy efficiency improves, the relevance of bound carbon in building materials will increase. The construction industry must contribute by decarbonizing building materials to achieve carbon neutrality by 2050. At Master Builders Solutions, we are committed to developing admixtures that will become key contributors and enablers in finding new, high-quality alternative materials that meet the construction industry's future demands.
2.1 The decarbonisation of the energy and steel industries
One solution which is available now and is widely used to reduce CO2 emissions in cement is to replace clinker with so-called SCMs. SCMs are sourced from the manufacture of iron and steel and also from coal combustion in the production of energy. The production of iron and steel accounts for 8% of global CO2 emissions, while burning coal in power stations accounts for 30% (2019, related figures taken from www.iae.org). To tackle the challenge of global warming, these industries will also be subjected to carbon reduction measures and will, either be decarbonized or phased out altogether. This will significantly impact the supply of related by-products, such as the SCMs granulated slag and fly ash.
The decarbonization of iron and steel manufacturing is being carried out by transitioning from blast furnace-based coal production to hydrogen-based direct reduction of iron. Pilot projects on an industrial scale have been successful, and the first plants will be constructed in the middle of this decade. This will significantly decrease the supply of granulated slag, which will not longer be available to produce low carbon footprint types of cement. It is not yet clear whether the properties of the new slag are suitable for producing concrete. For coal-fired power plants and hence for fly ash production, the situation is even more dramatic. In Europe, they are to be completely phased out by 2038 and as a result the by-product fly ash will be eliminated.
The EU and North America together consume around 30 million tons of granulated blast furnace slag and 20 million tons of fly ash in cementitious applications annually. Their efficiency with respect to mechanical and durability aspects can be expressed by the k-factor defined in the European concrete standard EN 206. They are 0.6 for granulated blast furnace slag and 0.4 for fly ash. Applying these factors and considering that 780 kg of CO2 are emitted per ton of ordinary Portland cement, annual CO2 savings of around 20 million tons are at risk. This is substantial, especially because the concrete industry has been tasked to reduce its CO2 footprint. We will see an increase in demand for alternative raw materials and/or approaches to concrete formulation.
Current attempts at this include increasing the proportion of limestone as the main cement constituent or exploring calcined clay as an ingredient. MasterCem products support these developments during cement production, while MasterCO2re, MasterEase and MasterX-Seed STE are specifically designed to address the related implications on the reliability, quality and consistency of concrete mixes.
2.2 Aggregate scarcity: The world is running out of high-quality material for concrete
The most significant proportion of concrete by weight and volume is aggregates which consequently have a significant influence on concrete properties. The proportion and strength of the aggregate itself determines strength and durability. The higher the degree of space-filling and strength and degree of inertness from well-graded particles, the stronger and more durable the concrete. Shape and texture also have an impact but are more related to workability. A combination of compact shape and smooth surface best accommodates the relative movement of grains and is a vital ingredient in high-quality concrete.
MasterSuna: Superplasticizer for challenging raw materials
Aggregates of the aforementioned quality can be mainly found and exploited along riverbeds and coastlines but these areas are often densely populated, therefore exploiting new sources is becoming difficult. Additionally, dredging in these areas harms ecosystems and biodiversity. Consequently, it is being progressively restricted by legislation. Finally, the extraction of natural resources far exceeds the renewal rate, as the United Nations Environment Programme (UNEP)’s 2019 report mentions.
The use of existing pits and quarries will need to be maximized and alternatives developed. One limit to the suitability of aggregates for use in concrete is clay contamination. It can severely affect the usability of entire deposits. Coarse aggregates can be washed, but for sand, this would be too costly. MasterSuna SBS is a technology that allows clay-contaminated fine aggregates which would otherwise be disregarded, to be used in the manufacture of concrete, transforming them into a valuable resource. Moreover, it extends the lifetime of affected pits and quarries and, where applicable, will also save water by reducing the number of aggregate washing cycles. Read about the success story of BRONZO PERASSO, a concrete producer, on this page.
Coarse aggregate crushed from rock as an alternative to natural sand can also be used but it is less suitable because it negatively impacts the properties of the concrete. Under similar conditions, concrete with crushed sand is more difficult to manipulate with workability retention reduced and property uniformity more challenging to control. Similar observations have been made when recycled concrete is used as the coarse aggregate. In both cases, MasterSuna RCA can overcome these drawbacks and increase the reliability of concrete made with these alternative aggregates, paving the way towards the circular economy.
2.3 The cost of waste disposal
The construction industry is wasteful and needs to become more efficient. According to the European Commission, it accounts for over one-third of all mineral waste with concrete and masonry representing the most significant proportion. To address this issue, new regulations have been implemented (EU Construction and Demolition Waste Protocol and Guidelines) or are being considered (construction and demolition waste) by the Environmental Protection Agency in the US. To encourage waste reduction and recycling, legislation that taxes and limits construction waste disposal has been introduced.
As a result, disposal costs for construction waste have increased by up to 100 €/m³ and are expected to increase further which will increase the recycling rate substantially. However, vast volumes of mineral waste are already used as a base for roads, pavements, backfill, and landscaping in downcycling processes. The factors that prohibit recycling are the relatively low cost and availability of naturally occurring aggregates which as we have explained will change, and the uncertain quality of concrete when recycled materials are used.
Concrete admixtures enable the use of recycled materials to reliably manufacture quality concrete. The superplasticizer MasterEase SBS maintains the workability of concrete despite the use of cement containing alternative materials limestone, calcined clay or recycled concrete fines (see cement standard EN 197-5 and upcoming standard EN 197-6). MasterSuna RCA enables the use of higher proportions of recycled concrete aggregates while reliably keeping concrete workability over time. Both superplasticizers increase the acceptance of concrete containing recycled concrete and support the industry in preserving our natural resources.
2.4 Efficiency increase in construction – the role of digitalization
When compared to previous times, standard building practices today, have not changed much and compared to other commercial sectors, productivity gains have been very low. This was highlighted in a recent high-level Construction Forum webinar. From 1947 to 2010, the gross value added per work hour increased by a factor of 16.1 in agriculture and 8.6 in manufacturing but it only grew by a factor of 1.1 in construction. There are many reasons for this which may include the inability to innovate, fragmentation (many small companies and trades), low margins, the availability of cheap labor and many stakeholders. The urgent need to decarbonize will hopefully trigger innovation and enable the adoption of new technologies where digitalization and automation will also play a key role.
3D printing of concrete structures is a technology in it´s early stages of development. Pilot projects have been completed in much shorter time frames and with improved material efficiency, but there is still a long way to go and chemical admixtures will be playing a key supporting role. Superplasticizers and viscosity modifying agents ensure the required workability profiles up to and during placing. At the same time, set retarders and hardening accelerators control the reaction of the cement and enable the required setting and strength development immediately after printing.
Remote quality control is further new technology that is currently being explored. Digitally determined concrete properties (predominantly workability characteristics) and the exact composition are formulated online and automatically corrected when deviations from target values are measured. In a more advanced stage, even the extrapolation of concrete strength will be possible using artificial intelligence.
The following ecological and commercial benefits can be achieved:
-
Efficient production to lower energy demand and material savings
-
More reliable concrete batches
-
Reduction in the number of reject batches to reduce transport, disposal costs and save material
When the standard deviation of strength properties is reduced, the safety margin related to the cement dosage required to achieve the desired strength is lower, which will reduce the carbon footprint of concrete batches. Chemical admixtures will be the solution as even in small quantities, they immediately and efficiently modify the properties of concrete even with lower cement dosages. Our latest superplasticising technology MasterCO2re has this capability and gives concrete robust, uniform properties from mixing, placement through to final hardening. This unique admixture technology can reliably control the impact of low-clinker, low CO2 cements which are modified with SCMs from diverse sources in varying temperatures which are being used more and more to improve the carbon footprint of projects.
Finally, digital tools will be required to accelerate coordination between construction processes. Building Information Modelling (BIM) is already being used to improve the efficient transfer of information for quicker, more reliable and transparent construction from the planning stage through the service life to the decommissioning phase of a building. Existing buildings will need to be catalogued in terms of the building materials used to facilitate circular construction by ensuring that after demolition, the remaining waste can be quickly and safely used in new construction.
2.5 Related blog articles
3. Low-Carbon Concrete
Terms such as “low-carbon concrete”, “sustainable concrete”, “green concrete”, “recycled concrete”, or “LC3 concrete” can be seen in the press and on the internet. Architects, engineers, contractors, and project owners must prove that they are able to meet sustainability commitments to clients and professional organizations like GCCA, Architecture 2030, Structural Engineers 2050 Challenge, the Carbon Leadership Forum, and the World Green Building Council. At Master Builders Solutions, we are convinced that this pressure will only increase and we are in close contact with our customers to ensure we offer solutions to meet their challenging sustainability targets.
3.1 The basis for sustainable concrete: clinker-reduced cement
At present so-called "supplementary cementitious materials" (SCMs) are either blended into cement or added to the mixer when concrete is produced as an alternative to cement clinker, the main source of embodied carbon in concrete. The cement option is widely adopted in countries applying EN standards – the UK being a prominent exception – the mixer option is used in countries relying on ASTM standards. As a result, the European standard series for cement, EN 197, specifies various cement types depending on quantity and types of SCMs. The clinker content largely determines the level of embodied carbon; the less, the better, although SCMs also come with a CO2 burden based on their source.
3.2 Cement types
In EN 197-1, types of cement are defined by clinker contents from 100% (CEM I) down to a minimum of 5% (CEM III/C), corresponding to a reduction of over 80%. What is actually available in any given local market depends on the availability of SCMs such as granulated blast furnace slag, fly ash or natural pozzolana (in descending order in terms of strength contribution). Accordingly, slag CEM III types of cement with high clinker replacement rates are generally sold in countries with iron production (e.g., Germany, Netherlands, Austria) and CEM IV types of cement with moderate replacement rates in those countries with natural pozzolana sources (e.g., Italy). Despite fly ash being widely available from coal-fired power plants, its utilization is still limited and when used, mainly in blended CEM II types of cement. Since this cement type, CEM ll allows the use of varying levels of SCM, it is the most widely used cement type today with clinker replacement rates ranging from 5% up to 35% (averaging around 25%), enabling a reduction of the embodied carbon of 20% compared to CEM I types.
Limestone and granulated blast furnace slag (inter-ground with clinker or added as ground material) are the most frequently used SCMs, followed by fly ash and natural pozzolana. Application rules for these types of cement are defined in the national application documents to the European concrete standard EN 206. Durability aspects particularly may lead to restrictions for one or the other cement type, but all things considered, low carbon concrete is already available today in, for example, buildings with low durability requirements, provided that the SCMs are available.
As the availability of suitable industrial by-products such as fly ash and granulated blast furnace slag cannot be ensured over the long term, new, alternative materials are needed, or the use of already accepted materials needs to be extended for cement production. In the context of cement production, the launch of EN 197-5 is essential. It defines two new, blended cement types: CEM II/C with further reduced clinker content (64% to 50%) compared to CEM II/A, CEM II/B and CEM VI cements with a clinker content of between 49% and 35%. For CEM ll/C cements, the accepted proportion of limestone in combination with pozzolanic or latent-hydraulic materials has been increased by up to 20%. For the other 3 cements mentioned, blended combinations of high proportions of granulated blast furnace slag in combination with other SCMs have been defined to replace cement clinker. Our game-changing admixture MasterCO2re is based on a new and highly efficient water reducing technology that compensates for strength loss and leads to uniform workability properties even if the quality of raw materials vary to provide a robust low-carbon concrete mix design. You can watch a short video that explains MasterCO2re in detail here.
In terms of new materials for cement production, EN 197-6 is already being worked on. It will facilitate the use of recycled concrete fines as the main constituent (up to 20%) in cement. This will further pave the way towards a truly circular economy in concrete construction. Another promising development is the so-called LC3 cement, which is a combination of cement clinker and a blend of calcined clay and limestone. The interaction between the clay’s aluminates and the limestone’s calcium carbonate is advantageous to strength development. Accordingly, and dependent on the quality of clay, clinker content as low as 35% appears to be feasible. If this succeeds, an eco-friendly alternative to granulated blast furnace slag in cement would be the result, which offers enormous potential for the long term reduction of CO2 emissions because both limestone and clay are available globally in large quantities. For the North American market, blended types of cement are defined in ASTM C595 and AASHTO M240. Blends with limestone as the main constituent have been considered but market acceptance has remained limited. Recently triggered by a cement shortage, limestone blends have become increasingly accepted, contributing to the decarbonization of the North American cement industry.
If we look at the performance of concrete containing low clinker cement types new challenges arise because they typically harm the workability and strength performance of the concrete. If we add variations of naturally based supplementary cementitious materials and chemical and mineralogical compositions, they affect the water demand of concrete and their interaction with admixtures. To counter these disadvantages MasterCem performance enhancers are added to the cement. Powerful concrete admixtures such as MasterCO2re maintain excellent workability characteristics, while Master X-Seed boosts the compressive strength of concrete in both the early and late hardening stages.
3.3 Low carbon concrete - pushing Co2 reduction to the Limit
The design of a concrete mix will typically follow a prescriptive approach with workability and strength requirements being determined by the mixing and placing conditions in conjunction with structural design requirements. Whether the given specifications are met can be easily tested but durability is difficult to predict. Specifications have been developed to incorporate long-term durability experience into mixes. Accordingly, a maximum water-cement ratio and a minimum cement content are usually contained in concrete testing standards such as EN 206 or ACI 318. Moreover, the authorized maximum dosage of SCMs or the number of fines that can be added are pre-defined for each cement type.
Calculate your carbon footprint with our ECO2Now Concrete Calculator app. Learn more on this page.
Regarding carbon footprint reduction, the use of cement containing SCMs instead of cement clinker is self-explanatory because they have a lower specific carbon footprint. However, as performance in terms of microstructure and the resulting strength development is not at the same level, higher cement dosages are frequently applied to achieve specified strength levels, which is then counterproductive in terms of carbon reduction. To overcome this, hardening accelerators such as Master X-Seed STE are applied to compensate for strength losses due to the inclusion of the SCMs. Moreover, if minimum cement or maximum SCM dosages are not yet exhausted at target strength, a further reduction of cement may be possible with the associated reduction in carbon emissions.
This provides a safe, yet robust and rigid framework for the design of concrete mixes but this method, even with efficient material utilization cannot fulfill the full potential of carbon footprint reductions. To facilitate the further development of sustainable solutions, performance-driven design concepts for durability have been developed and are contained in the European concrete standard EN 206. They involve the testing of durability parameters such as chloride migration and carbonation in concrete for mixes that do not meet minimum cement requirements compared to accepted mix designs under similar exposure conditions.
3.4 Saving water
To minimize cement clinker and the resulting CO2 content without excessively influencing the strength profile, the water/cement-ratio (w/c) must remain constant by proportionally reducing the cement and water dosages by the same ratio. To maximize the reduction of CO2 the majority of the fillers should consist of natural materials such as limestone. Tests have shown that the minimum water content required for mixes with acceptable workability properties is 130 kg/m³. This compares to a standard water requirement of 160 – 170 kg/m³, a saving of 19% to 23%.
If we take a concrete mix with CEM II/A as a starting point, a reduction in the carbon footprint of between 40% - 50% can be achieved. Concrete workability is affected when inert, natural fillers replace water and cement as these mixes are more viscous. Specifically designed concrete admixtures such as MasterCO2re and MasterEase adjust the viscosity of sustainable concrete mixes to fully achieve currently accepted placement and manipulation quality standards. MasterSphere reliably maintains the durability of concrete with respect to freeze-thaw resistance. It provides the required expansion space for freezing water and ensures the integrity of concrete in cold and wet climatic conditions. Finally, low-carbon concrete is not only environmentally friendly but is a cost-neutral alternative to conventional concrete.
3.5 Geopolymer concrete: Eco-friendly concrete without cement
Geopolymer concrete (GPC) contains aggregates just like normal concrete but no cement. It has been widely researched over the past few year and has been experiencing tremendous interest because it contains no clinker and therefore, fundamentally differs from traditional concrete.
The binder consists of SCMs such as fly ash, slag, calcined clays, silica fume or pozzolans. An alkaline activator is then added to initiate a so-called “inorganic polymerization”, the chemical reaction that hardens the concrete. Geopolymer concrete technology offers a variety of mix design options due to the many possible combinations of binders and activators that can be used. It will remain a sustainable concrete because of the absence of clinker (cement) as a binder and will save enormous amounts of CO2 for customers to achieve better BREEAM or LEED certifications.
Concrete composition in comparison, cement-based vs. geopolymer concrete
.jpg?width=400&height=210&name=20231214_GraphicCBC_Draft%20(1).jpg)
.jpg?width=400&height=210&name=20231214_GraphicGPC_Draft%20(1).jpg)
The mechanical properties of geopolymer concrete are determined by many factors including the water/binder-ratio, binder type or paste volume as well as the choice of alkaline activator and curing method. A highlight of GPC is the high resistance to chloride, sulfate, and acid attack, demonstrating exceptional durability under severe conditions.
Geopolymer concrete main benefits:
- Reduced CO2 concrete footprint through utilization of SCMs
- The use of industrial waste and by-products (SCMs) to preserve natural resources and the environment
- Enhanced durability to reduce maintenance costs and increase the service life for specific applications
- Improved surface aesthetics due to the absence of Portland cement-related efflorescence
The many benefits of GPC can be specifically targeted for ready mix, site mix, precast, and manufactured concrete products (MCP) specific applications.
3.6 Fiber-reinforced concrete – a lightweight and user-friendly solution
Concrete is brittle and traditionally has been reinforced with steel to give it the necessary flexible strength or "ductility". Steel is however expensive, difficult to process and transport, it is also responsible for a large amount of CO2 emissions. MasterFiber, the range of lightweight, synthetic macro fibers benefits concrete producers with an alternative reinforcement solution that can partially or entirely replace steel.
MasterFiber at a glance:
-
Improved ductility of concrete structures
-
Improved crack control
-
Replacement of steel
-
Reduced plastic and drying shrinkage
-
More efficient application
The addition of fibers to concrete improves the structural performance of hardened concrete at a very early stage. Fibers control plastic and drying shrinkage cracking and improve the structural response to tension, bending and shear while providing ductile strength. The improved impact resistance of the concrete makes it more resistance to fatigue and therefore more durable with limited fire protection advantages. Synthetic fibers are non-magnetic, 100% alkali resistant and are corrosion-free. The importance of fibers is growing because through the replacement of steel and increased durability has brought them into focus for reasons of sustainability.
4. Efficiency Through Concrete Admixtures
The construction sector faces the challenges of committing to sustainable construction whilst coping with tight time schedules, meeting high-quality standards and being generally more efficient. There has been little or no improvement in the construction industry's gross value creation per working hour for a long time and pressure to improve processes is growing. Advanced concrete admixture technology will support process improvement and the commitment to sustainable construction.
4.1 Ready mix concrete: Admixtures speed up your construction process
Ready-mix concrete is produced at centrally situated concrete manufacturing plants and delivered to the construction site by mixer trucks. Three factors determine the quality of concrete: Constant and uniform composition to guarantee strength in the hardened state, specific workability characteristics including flowability, viscosity, finitisability and retention over time during transport, and finally pouring and placement. Long transport distances and high temperatures can affect flowability, making the concrete tougher and stickier and therefore, more difficult to pump and place. This often results in concrete batches being rejected on arrival which costs time and money and results in the inefficient use of materials with additional transport and waste disposal costs.
MasterCO2re and MasterEase viscosity modifying superplasticizers improve the rheological properties of ready-mix concrete throughout the entire process from mixing, transportation though to placement especially in hot climatic conditions. This reduces the risk of reject batches and uncontrolled on-site water addition. Maintaining lower water content results in higher quality concrete with improved durability. MasterEase lowers plastic viscosity by up to 30%, significantly reducing the pressure needed to pump concrete. Placing and smoothing are much easier, faster, and more economical. Moreover, the abrasion of mixers, pumps, and pipelines is reduced, leading to less downtime and lower maintenance costs.
Master X-Seed, on the other hand, accelerates the hardening of concrete even in low winter temperatures and possesses considerable time-saving benefits. The admixture is based on a unique CSH (calcium silicate hydrate) seeding technology that promotes the natural hydration process of the cement to ensure rapid early strength development and hence provide sufficient resistance to freezing. For example, Master X-Seed was vital in constructing the 155-meter-high Marienturm in Frankfurt, Germany. Under a tight schedule, Master X-Seed enabled each of the 38 floors to be built in just six days with consistent high quality and fast construction progress being achieved even during the winter months. A further example of the efficient use of ready-mix concrete with Master X-Seed is industrial flooring. The time between pouring and finishing can be reduced considerably when this technology is applied to minimize factory downtimes and production stoppages.
The Construction of Marienturm in Frankfurt - with Master X-Seed.
4.2 Precast concrete manufacturing: Efficient, safe and circular with a reduced carbon footprint
As the name indicates, precast concrete elements such as beams, walls, slabs, façade elements or concrete utilities are manufactured in a prefabrication plant under industrial conditions. They are shipped to the site by truck and assembled in-situ. Production is independent of weather conditions and processes are documented, optimized and controlled. The creation of steel reinforcement and its positioning is often automated. The concrete is centrally mixed and the quality is constantly monitored. It is distributed to the place of casting within clearly specified time periods. Curing is controlled so that the demolding of elements and the cleaning of formwork takes place within a 24-hour period for a 1-day production cycle. The production process is very efficient and in addition, the work environment is safer and healthier for the workforce compared to a construction site.
Precast elements save time due to shorter installation times with uniform, high-quality, durable elements benefiting both the contractor and the owner. The weight and size of the precast elements will determine the transport and placing constraints. Modular building elements which are fully equipped with water and power installations, for connection on-site can replace local construction. Material-efficient design and higher-strength concrete for more slender structures will be possible.
If considered in the early planning stage, precast elements and modules can be designed to be dismantled and re-used for other purposes after their initial service life. In this way, the precast concrete industry is in the mid to long term in the position to enable circularity and waste reduction in construction.
To enable a daily production cycle, highly reactive types of cement with high clinker content are used with heat curing frequently applied. This directly or indirectly leads to high carbon emissions and increases unit costs. Energy demand will need to be reduced through the elimination heat curing. Mix design optimization through the use of clinker reduced cement types with SCMs is paramount to reduce CO2 emissions.
Unfortunately, per se, these measures would lead to a decrease in efficiency and concrete quality, as:
-
SCMs are less reactive than clinker leading to inadequate strength development for quick demolding
-
Extended heat curing to compensate for losses is not an option due to an increase in energy demand
-
Reduced water content to counteract strength losses and intrinsically higher water demand of fine SCMs put the workability required for quick and convenient placing at risk.
To enable the increased use of SCMs in applied cement or concrete types, the use of advanced superplasticizers and hardening acceleration technologies paired with mixed design expertise is required. MasterCO2re is based on a new and highly efficient water reducer technology that compensates for strength loss and enables uniform workability properties even if the quality of raw materials varies, providing a reliably robust low-carbon concrete mix design. For concrete mixes that are too sticky, MasterEase has been designed to reduce concrete viscosity. Finally, MasterX-Seed STE is a unique hardening accelerator which boosts concrete strength in the early stages (important for timely demolding and reduced energy input for curing) as well as at 28 days which is a mandatory requirement to meet specifications from a structural design and durability perspective.
In practice, precast plants have been switching cements from 80% clinker to CEM III/A slag cements with a clinker content of around 50% for many years now. The regional development of lower clinker cements in cooperation with precast manufacturers demonstrates that a carbon footprint reduction of about 30 % in precast concrete is not out of scope.
4.3 Mastering the challenges of digitalization
The digitalization of the economy has accelerated in recent years and is increasingly shaping how we work and live in our everyday lives. The transformation is recognizable in all areas and the construction industry is no exception. 3D printing is emerging as a possible new construction method with the introduction of digital manufacturing processes in precast new perspectives in the design of buildings are being opened up.
3D printing can change the way concrete is produced and place which will allow for improved construction efficiency because it is faster, less cost-intensive, safer, resource-saving and offers more consistent quality. This will require expert knowledge in composition and admixture technology but it is also a complex field in relation to the physics and chemistry of materials. It differs fundamentally from conventional construction processes but presents concrete companies with new opportunities particularly in the production of formwork or the manufacture of concrete elements.
Challenges that must be mastered are concrete pumping, placing, and hardening. All concrete must be pumped over long distances of up to 40 meters, requiring the exact rheology for the concrete to pass through the nozzle. When printed, the placed concrete should generate sufficient strength and not sag in order to accommodate the next layer. It should set immediately while keeping its shape so that no formwork is needed.
The control of setting and hardening requires detailed knowledge about concrete reaction mechanisms and applying an appropriate accelerator at the right time. Using a wide range of our superplasticizers, R&D work is progressing and vertical build-up rates of several meters per hour with CO2-optimized concrete mixes has already been achieved. There is a good chance that 3D printing will become a resource-saving and carbon-reduced construction method.
Benefits you do not want to miss:
-
Fast construction progress
-
No limitations in design with custom concrete
-
Less labor and the elimination of formwork to reduce costs
-
Resource and CO2 emission savings
Self-compacting concrete (SCC), also widely known as self-consolidating concrete, is an advanced concrete technology. It is characterized by extraordinary fluidity and at the same time, non-segregating behavior. When cast, SCC is self-levelling and releases air without vibration or any other compaction method to leave a superior surface quality. It is commonly used to cast complex concrete structures, e.g. façade or heavily reinforced elements where conventional compaction methods cannot be applied. Another motivation is to eliminate compaction and finishing for the sake of increased production efficiency and/or improved working conditions with respect to workers’ health.
Main benefits of self-compacting concrete:
-
Fast and more straightforward concrete placement and construction
-
Flows into place without the need for mechanical consolidation
-
Reduced labor cost since no concrete vibration is needed
-
Increased safety on the job site
-
Excellent finished surface quality
4.5 Relevant blog articles
5. Project References: Low-Carbon Concrete Construction
One World Trade Center, or the Barcelona Harbor, concrete is the common primary construction material of these buildings. Buildings and infrastructure projects of such scale would not be feasible and would not meet today's sustainability standards and targets without the help of concrete admixtures. Modern admixture technologies enable the production of robust, clinker-efficient concrete which is often referred to as "green concrete". The effectiveness and efficiency of these new, innovative technologies has been proven in some prominent projects:
5.1 The EDGE East Side Tower in Berlin, Germany
At 140 meters high, the EDGE East Side Berlin will be the tallest office building in Berlin. Master Builders Solution has developed a suite of products to improve the workability of low-clinker concrete. This enabled this benchmark project to be constructed with 50% less CO2 emissions compared to conventional concretes. The concrete was successfully pumped over a total distance of 275 meters, 140 meters of which were vertical. Our state-of-the-art solution, MasterSuna SBS 6080 ensured uniform and robust concrete workability even during hot summer days. Upon completion, the EDGE East Side Berlin was certified Platinum by the German Sustainable Building Council.
5.2 One World Trade Center, New York City, USA
Sustainability was one of the main criteria in constructing the 541-meter-high skyscraper. The New York/New Jersey Port Authority insisted on strict requirements for replacing Portland cement with supplementary cementitious materials (SCMs). At the same time, it was essential to achieve a compressive strength of up to 97 MPa which required a special high-quality ready-mix concrete. Our customized Green Sense Concrete technology was chosen as it optimizes concrete mixes in terms of environmental friendliness, concrete performance, and production costs. Thanks to special admixtures, 71% of Portland cement was replaced with SCMs to achieve a significantly reduced environmental impact as validated by an eco-efficiency analysis. This saved a remarkable 15,000 t of carbon emissions, 25,000,000 kWh of energy and 500,000 kg of fossil fuels.
5.3 Paving of the ICL Port Terminal in Barcelona, Spain
The new salt and potash shipping terminal for Tramer, an ICL company is located at the Álvarez de la Campa dock in the Port of Barcelona. The project included the ground reinforcement of 60,000 m2 for two new warehouses as well as the outdoor terminals. The concrete was subject to the stringent requirements of withstanding heavy storage loads, resisting chloride attack from the stored salt and the marine environment whilst ensuring high durability. A decision was made to use non-corrosive polymer fibers for the concrete reinforcement because steel would corrode very quickly under these conditions. The superplasticizer, MasterEase was used to control rheology and to maintain workability. The reduction in the use of steel and the increased durability has brought significant advantages in terms of sustainable performance.
Any Questions?
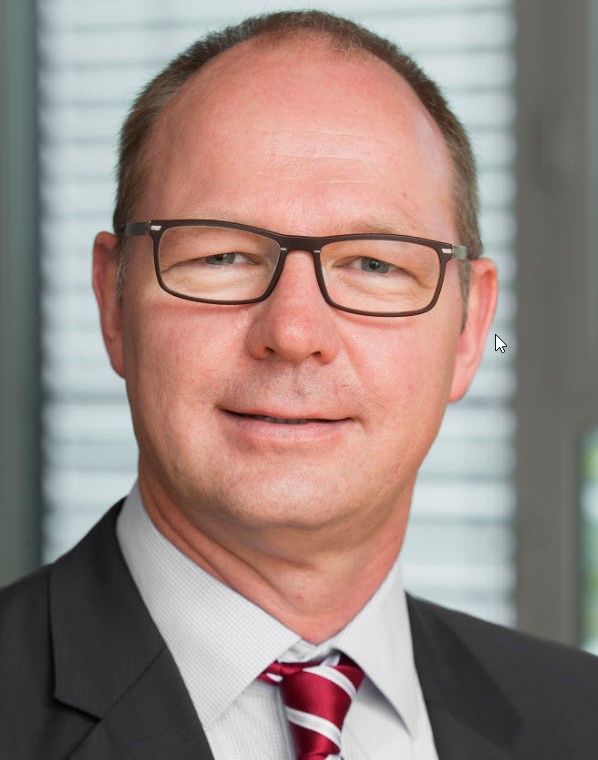